

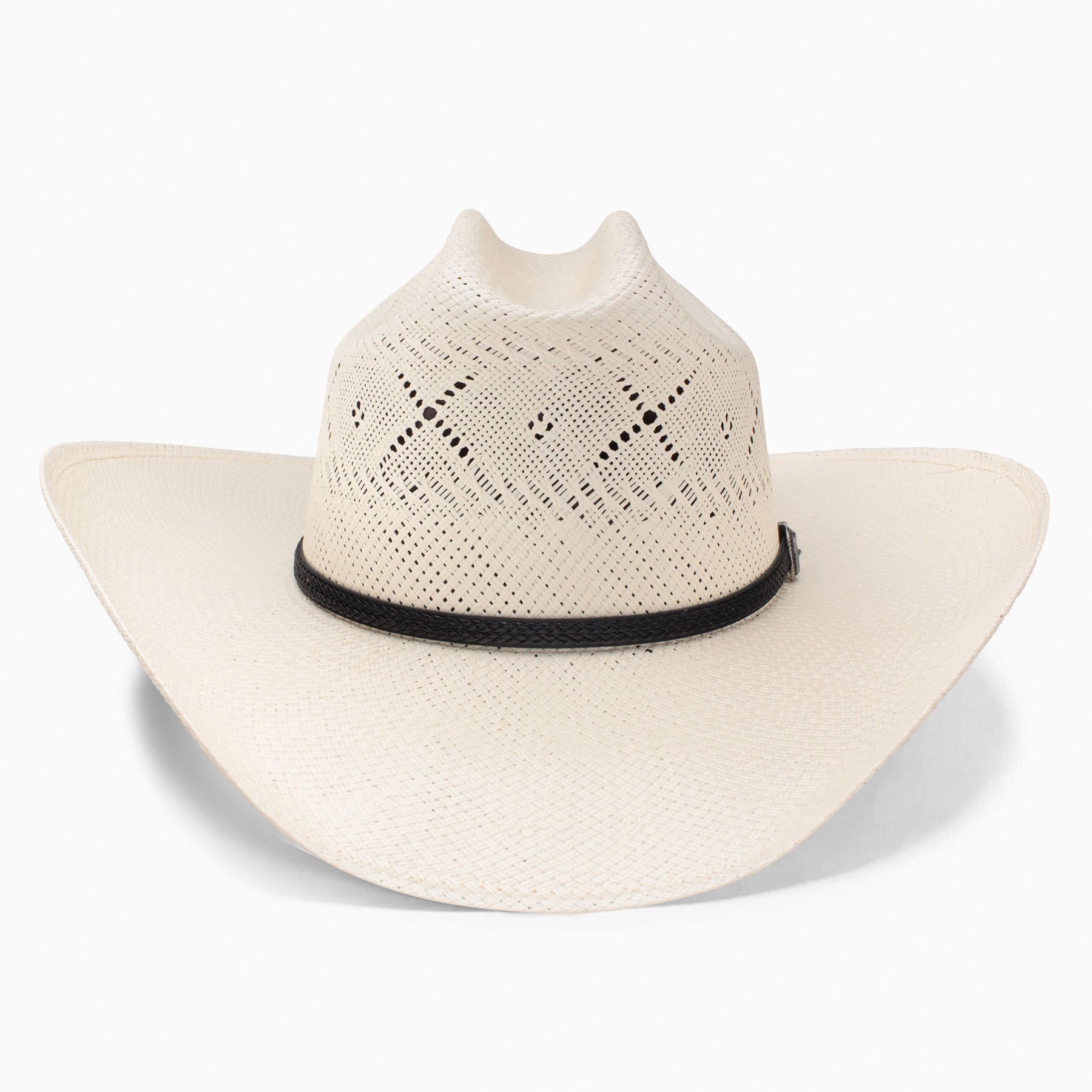
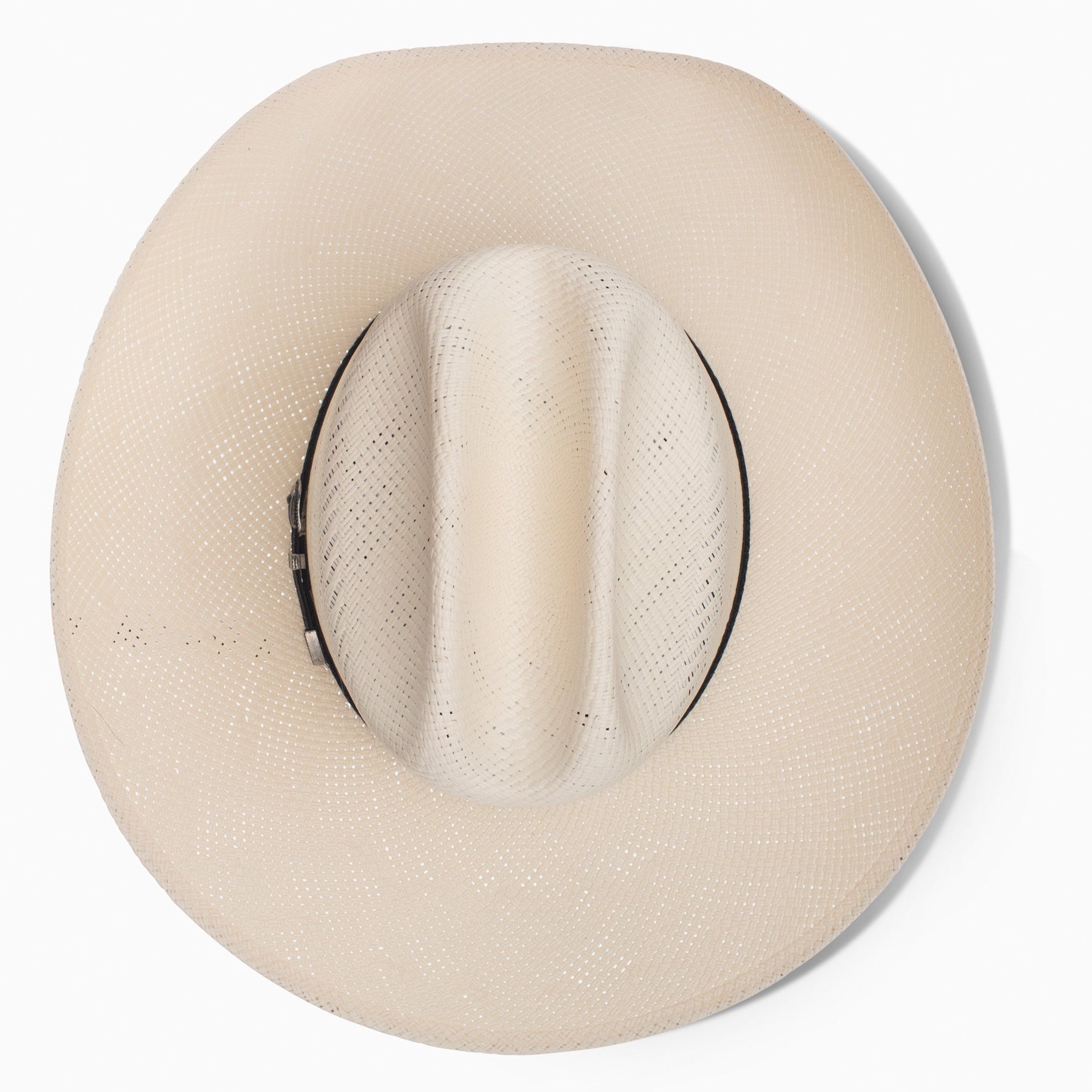
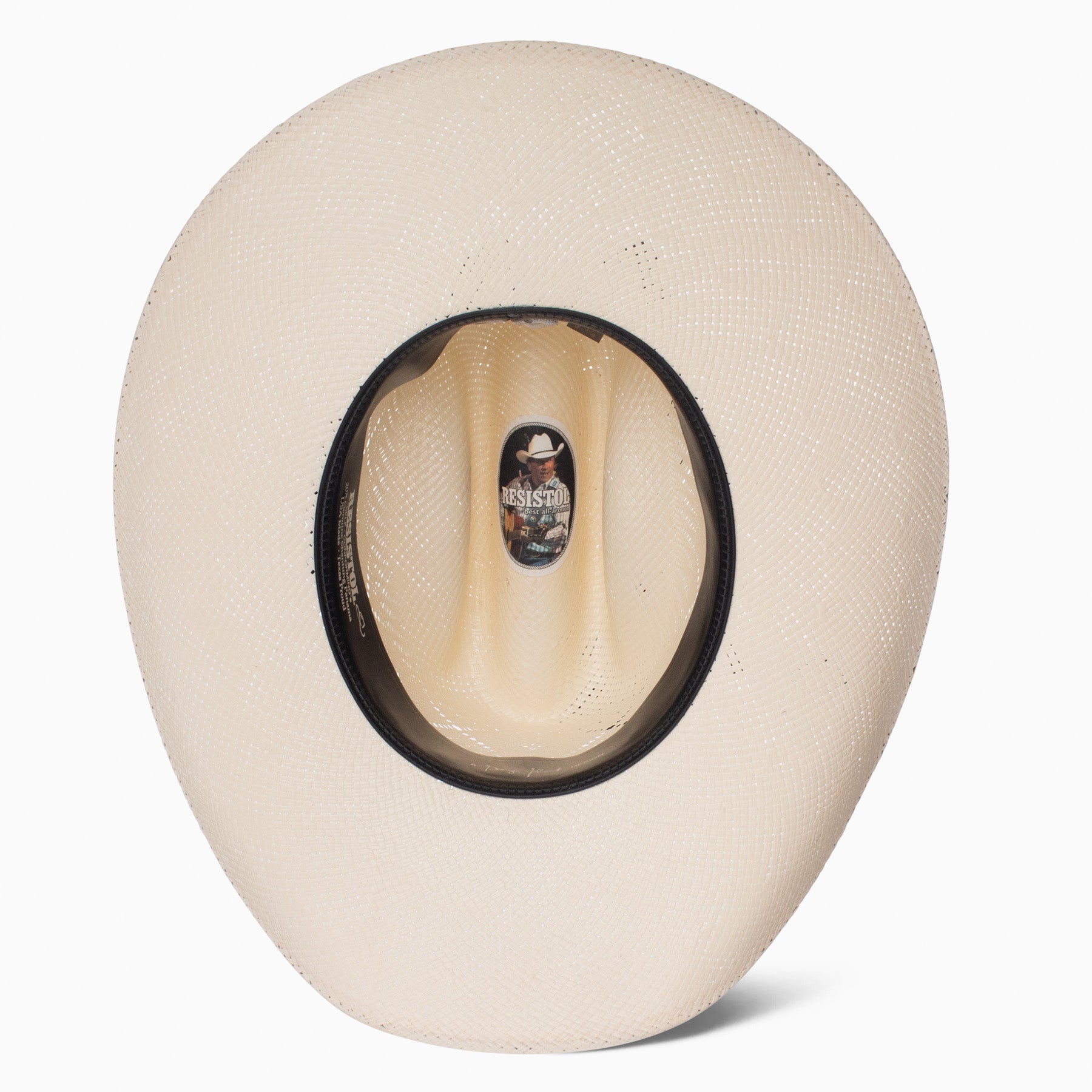
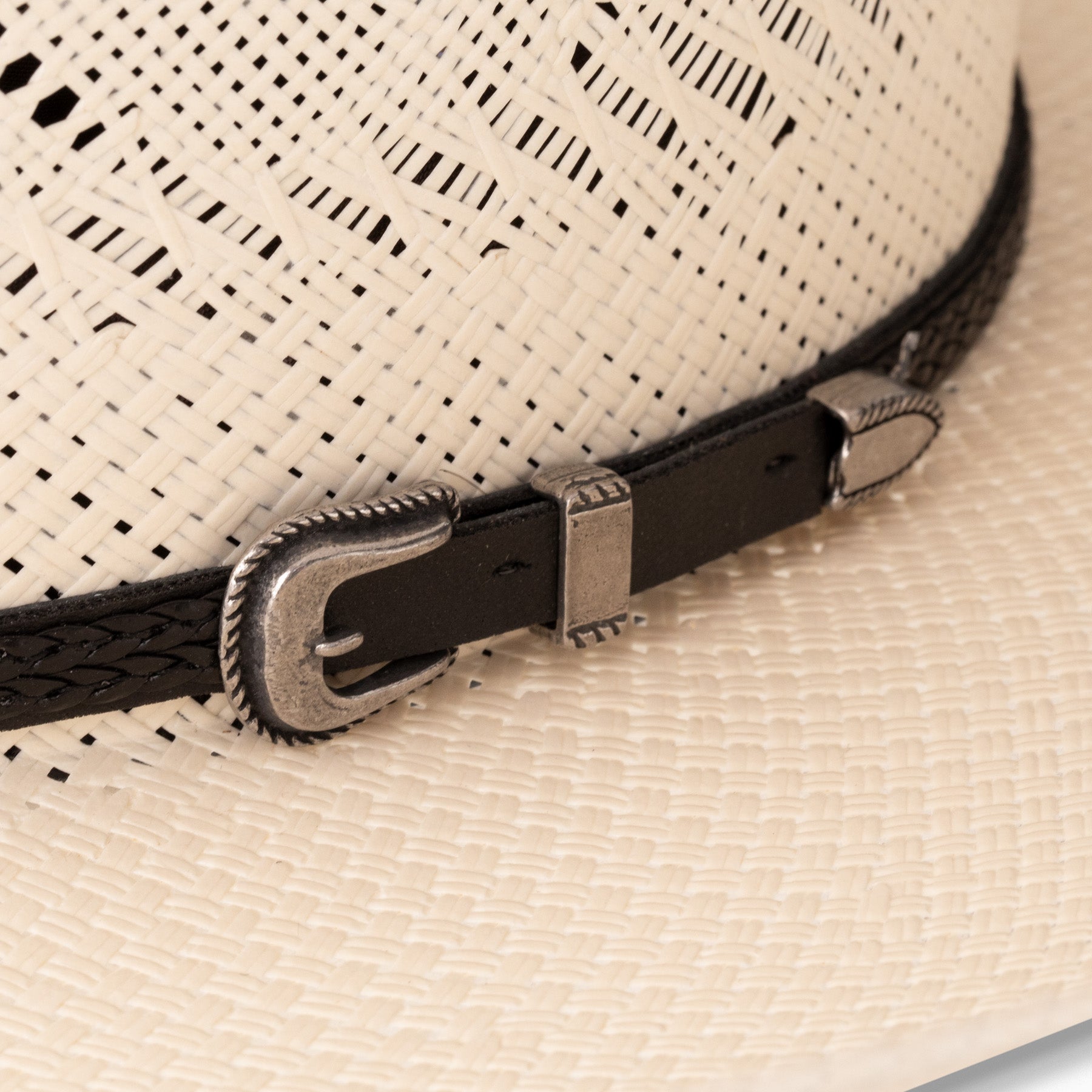
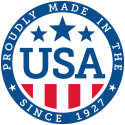
George Strait 20X All My Ex's Straw Hat
Part of Resistol’s George Strait Collection, this dazzler of a straw hat boasts 20X quality, a 4 5/8” cattleman’s crown, a 4 1/4" brim, a leather sweatband, and a brown woven hatband with a silver buckle. This hat is good looking enough to attract your next ex, Cowboy. Consider yourself warned.
Choose options


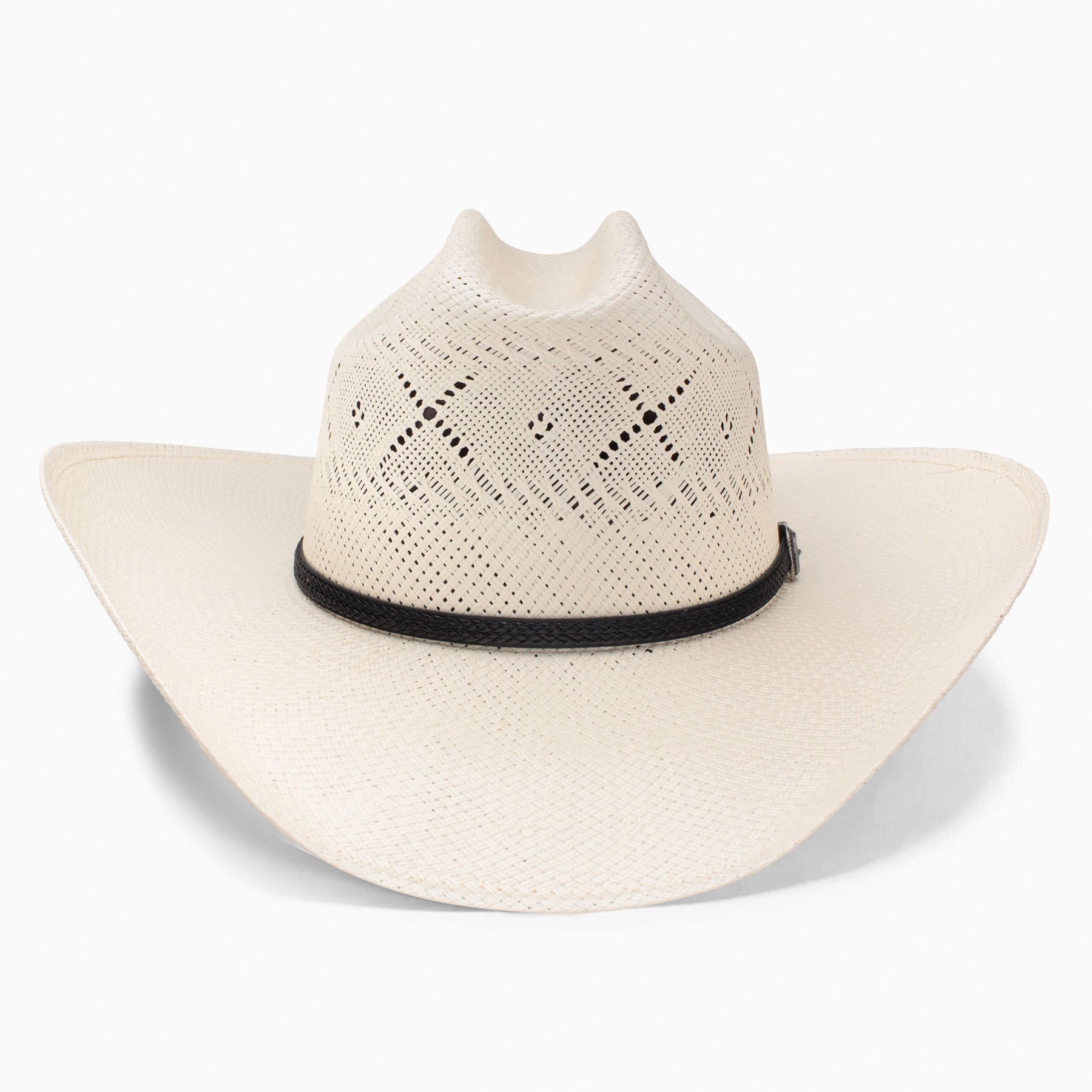
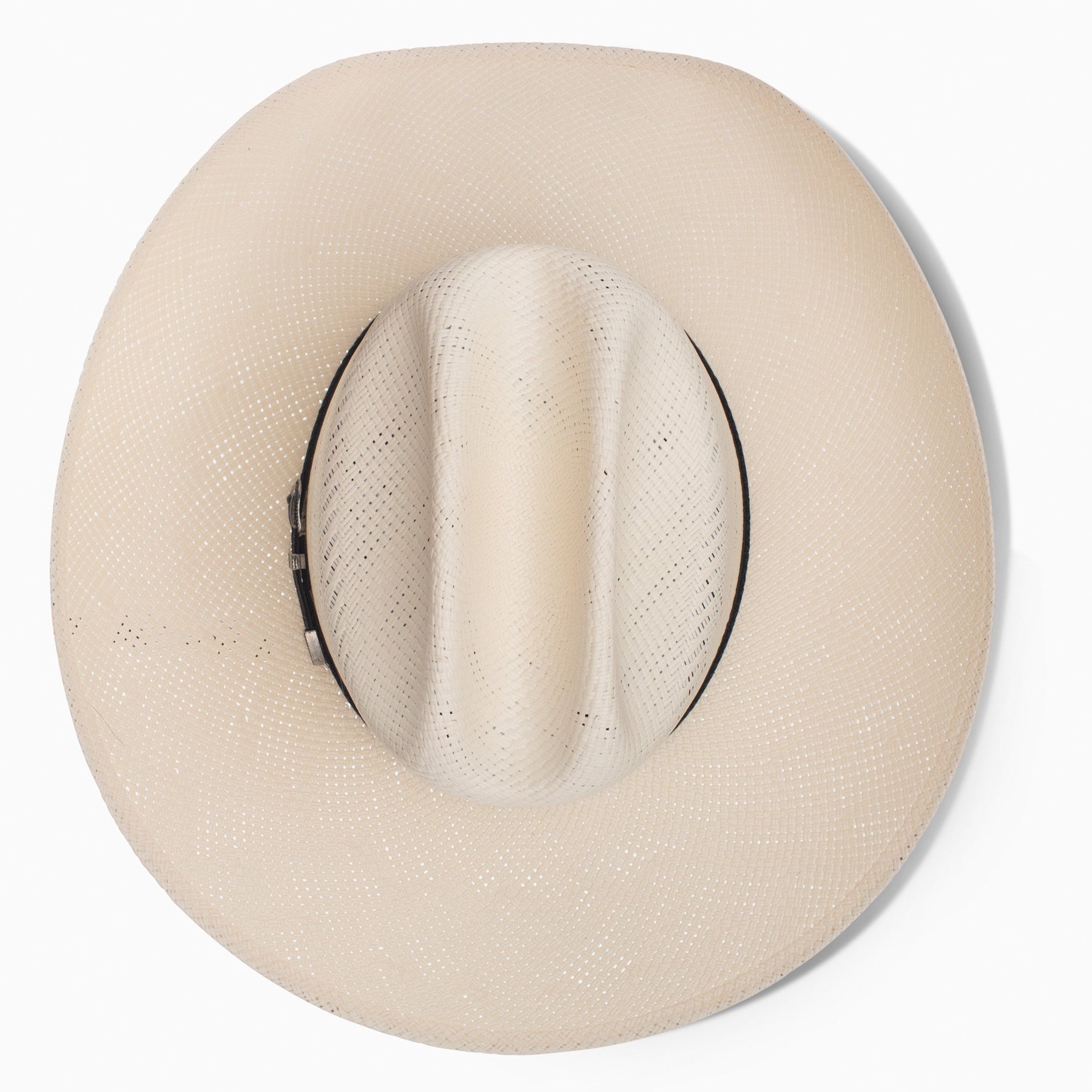
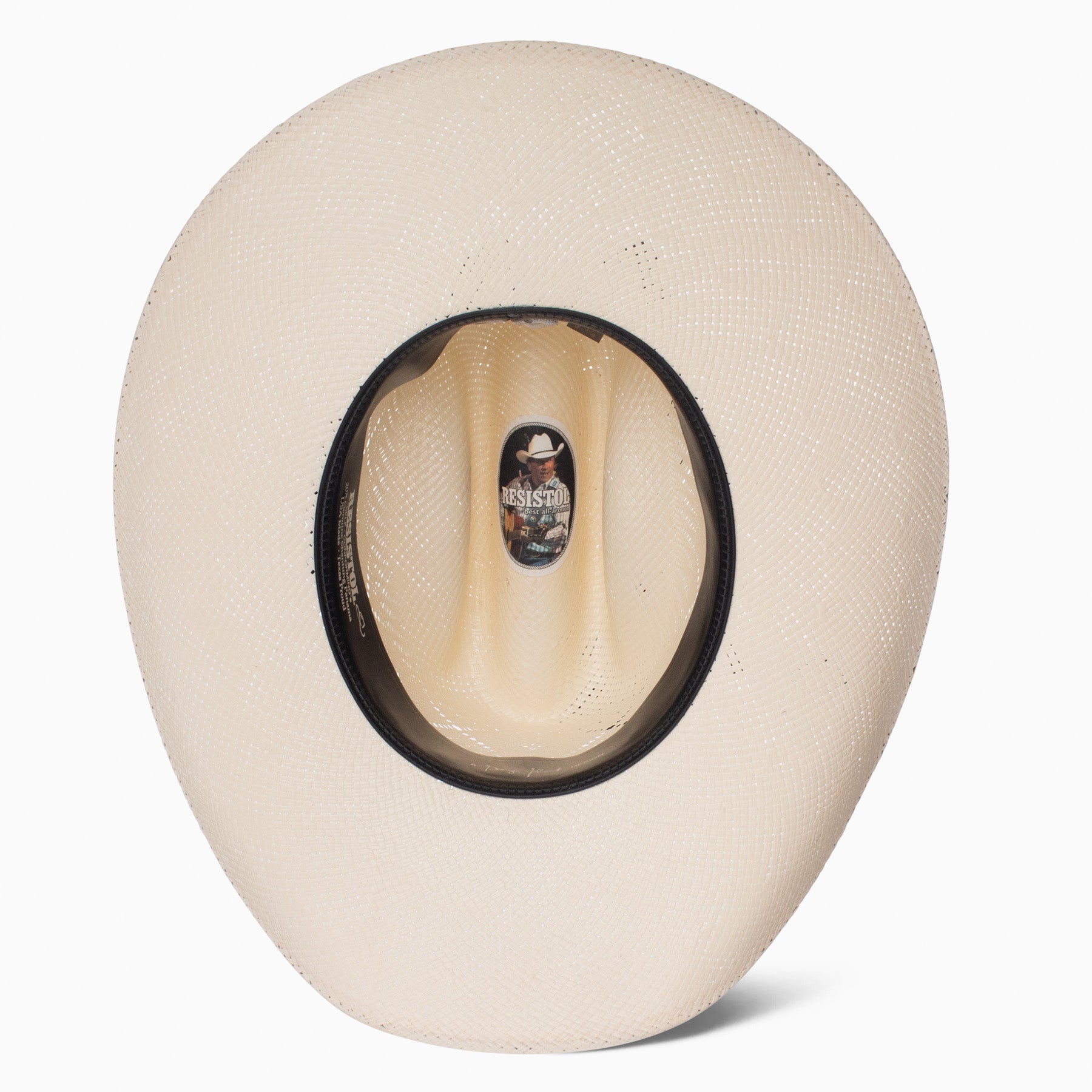
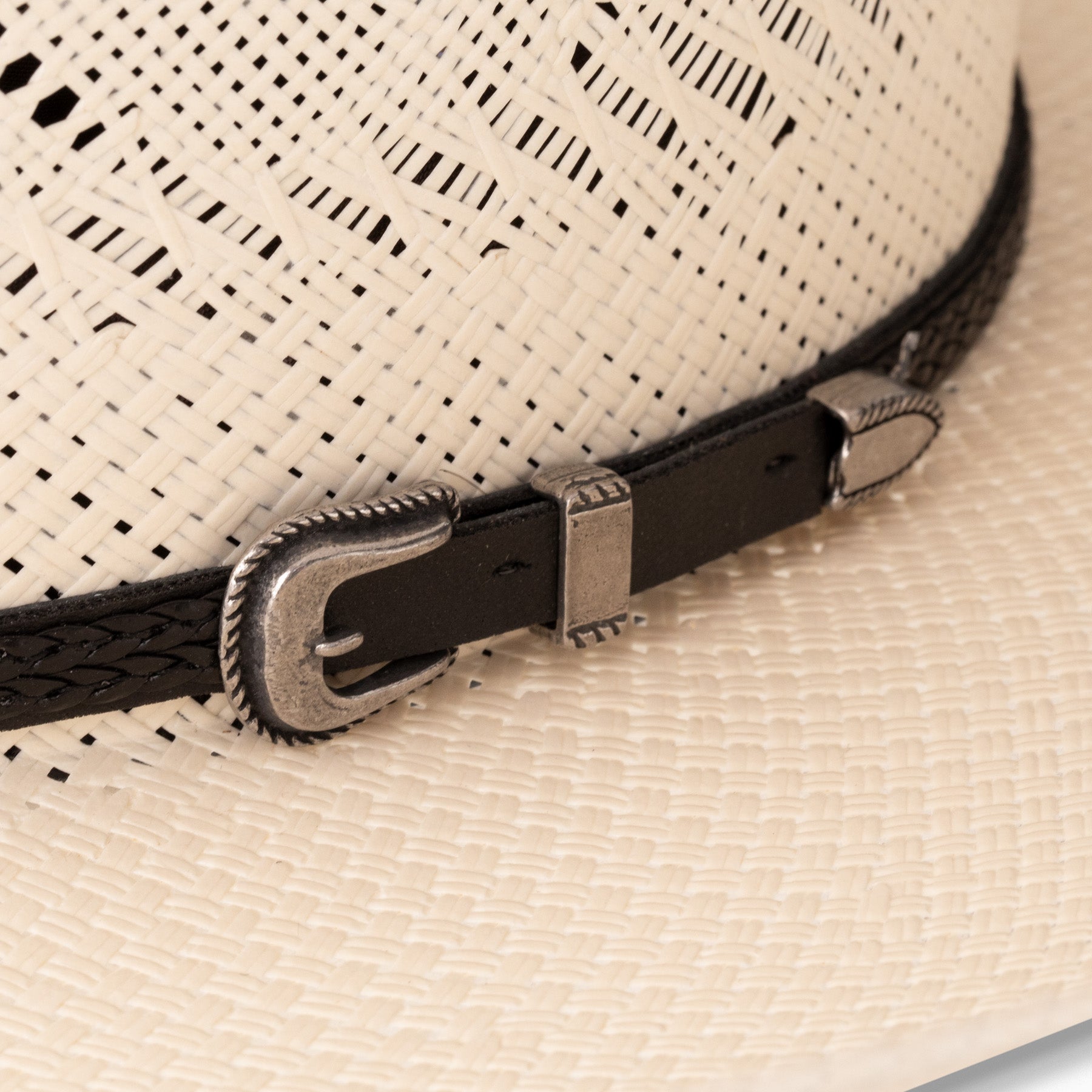
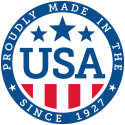
George Strait 20X All My Ex's Straw Hat
Sale price$200.00